How can you define product quantities when high sales last only one day? How can you ensure that your customers will get everything they need? Is it possible to automate some processes to ensure that your inventory has enough products? Here, we'll answer these questions and show you how to manage it from Odoo.
Carlos owns the Cardenal chain of boutiques, with branches throughout Latin America. Throughout its history, one day before Mother's Day, sales increase by at least 200 percent in each store.
He uses the Just-in-Time (JIT) method for inventory management because he knows that this way he can produce only what is needed, in the quantity needed, and at the time needed. This Japanese system, created in 1950, based on demand, seeks to reduce waste, improve product quality, and increase efficiency in the supply chain.
What are the benefits of implementing this 70-year-old method?
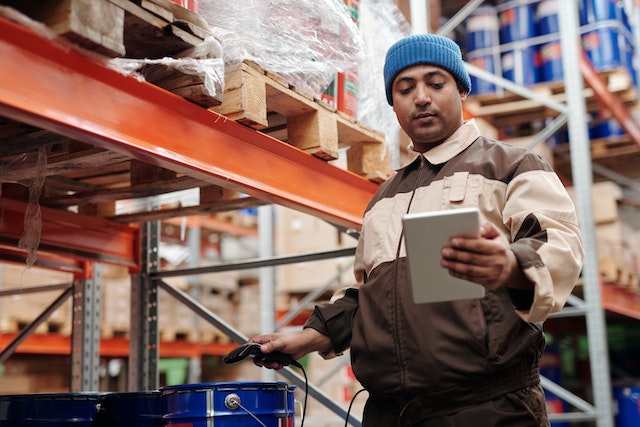
Cost reduction: JIT helps reduce costs by allowing companies to produce only what they need at the time they need it. By minimizing the amount of inventory stored in the warehouse, storage space is reduced, and costs associated with maintaining large amounts of inventory are reduced.
Increased efficiency: JIT improves the efficiency of the supply chain by allowing materials and components to be delivered just in time for production. This means that companies can minimize wait time and waste in production, improving quality and reducing costs.
Increased flexibility: JIT helps companies be more flexible by allowing them to adjust production to meet market demand. By producing only what is needed at the time it is needed, companies can adapt more quickly to changes in market demand.
Using the JIT method has allowed Carlos to guarantee product availability at all times, which has allowed him to meet the needs of his customers, position himself, and even open new branches.
Some concepts before continuing
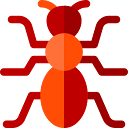
What is the minimum stock?
The minimum stock is the quantity of products that must be kept in inventory to ensure that there are always enough products available to meet demand. If the stock falls below the minimum, there is a risk of not being able to meet demand and losing sales.
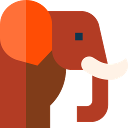
What is the maximum stock?
It is the maximum quantity of products that can be kept in inventory at any given time. Defining a maximum stock helps to avoid excess inventory, which can generate unnecessary storage costs and product obsolescence. In addition, having excess inventory can prevent the introduction of new products and reduce business profitability.
How to define my minimum and maximum stock?
Whether you have older sales points, with a history that makes it easy to define your minimum and maximum stock, or have a newly opened sales point, you need to ask yourself, "What is the quantity of products that I must have to allow me to provide service to my consumers, but not generate unnecessary storage expenses?"
There are mathematical formulas that you can use to define your minimum and maximum stock, as long as you have historical information from your stores or a market study. Of course, they can vary according to the demand for your product by high or low-demand dates, the frequency of purchases, the delivery time of suppliers, the production time of the product, among others.
To define the minimum stock quantity, you can use the Order Point (OP) formula, which is calculated using the formula:
OP = D * (LT + SS)
Where:
D = average daily demand for the product in units.
LT = average product delivery time in days.
SS = Safety stock in units (represents the minimum amount of inventory you must have to avoid running out of stock before a new order arrives).
To define the maximum quantity of products in inventory, you can use the formula for Maximum Stock (SM), which is calculated as follows:
SM = PP + CANT
Where CANT = Optimal order quantity in units (represents the quantity you should order to maximize efficiency and minimize costs).
Define your minimum and maximum values for special dates with Odoo.
You can adjust these values for high-demand dates such as Mother's Day or Christmas through the Demand Planner tool in your Odoo inventory module.
The 8 steps to define minimum and maximum stock values for special dates in Odoo:
Access the Inventory app in Odoo 16.
On the left menu, select the "Products" option.
Select the product for which you want to set minimum and maximum stock values.
Select the "Replenishment" tab at the top of the page.
Enter the minimum stock value in the corresponding field.
Enter the maximum stock value in the corresponding field.
In the "Procurement Planning" section, select "Make procurement planning for this product".
Select the "Minimum stock quantity" option from the dropdown menu and add the corresponding value. Then, select the "Maximum stock quantity" option and add the corresponding value.
But Carlos is clear that setting his minimum and maximum stock quantities is just the beginning of excellent inventory management. For days of extraordinary demand, he needs communication between his points of sale and inventory to be immediate.
To achieve real-time communication between Point of Sale, Inventory, and Purchasing every time one of these undergoes any movement, you can use the Odoo Enterprise Resource Planning software.
How to connect the Point of Sale module with Inventory in Odoo 16?
Linking these two applications will streamline your warehouse supply process, and this connection will allow you to register and subtract from your inventory immediately when you make a sale from your Point of Sale. Additionally, your Point of Sale will only display your actual available stock, thus avoiding the error of offering non-existent products to your customers.
Link your Odoo Inventory and Point of Sale modules in 7 steps:
Access the Inventory module.
Select the product you want to link to the Point of Sale module.
In the "Inventory" section of the product, make sure that the "Managed by Odoo Point of Sale" box is checked.
In the Point of Sale module, access the "Products" section.
Select the product you want to link to the Inventory module.
In the "Inventory" section of the product, make sure that the "Managed by Odoo Inventory" box is checked.
Save the changes made in both modules.
For a chain like Cardenal, it is very important to maintain contact with suppliers, know the delivery times of each input or product to make requests at the appropriate times.
When using the formulas we shared, you have already considered the minimum stock you need to have to have enough time to request inputs from your suppliers and replenish your warehouse.
To further streamline this work, automate your request for quotes from suppliers in less than 10 steps every time you reach your minimum stock through Odoo's Inventory module:
Access the Inventory module.
Select the product you want to configure to request a quote from suppliers.
In the "Inventory" section of the product, make sure that the "Managed by Odoo Purchases" box is checked.
In the same section, set a value in the "Minimum Stock" field. This value determines the minimum amount of stock that you want to keep in inventory for that product.
Save the changes made to the product.
In the "Odoo Purchases" module, access the "Configuration" section.
In the "Purchases" tab, make sure that the "Generate a request for a quote to the supplier when the minimum stock is reached" box is checked.
In the same section, make sure that the "Notify the internal user when a request for a quote to the supplier is generated" box is also checked.
Save the changes made to the Odoo Purchases module configuration.
There you go! In less than 10 steps, you will be able to automatically generate a request for a quote to the corresponding supplier when the stock of a product in Odoo Inventory reaches the value established in the "Minimum Stock" field. Additionally, you will receive a notification within the system to keep you informed of the generated quote request.
Setting your minimum and maximum values, automating communication between your different departments and suppliers, establishing specific criteria for your high or low demand seasons, in short, maintaining proper inventory management is crucial to the success of your business.
Technology solutions like the Odoo ERP can help simplify the process and improve efficiency. By implementing these best practices, companies can improve their profitability and gain a competitive advantage in the market.