Have you ever wondered: “Why are your delivery times so slow? " Or “Why is there always a work area in your company that is slower than the others?” This phenomenon is called a “bottleneck”, throughout this blog post we will explain why it happens, and we will offer you an alternative to solve it.
A "bottleneck" refers to some phase of the process in your company that makes the output of your product or service not able to be on time. We will explain it to you below with a simple example:
Imagine that in a metallurgy plant the process you are working with consists of three phases, A, B and C.
In phase A the process begins with the welder, he has the capacity and resources to weld 10 items per day.
Phase B is the second part of the process, here the collaborator is in charge of painting the items that have already been welded, this area only has the capacity and resources to paint 5 items per day, due to the slower process.
And finally there is phase C where they are responsible for packing the product. This area has the capacity to pack 15 products per day, but because phase B is slower, less product reaches this area. Do you notice where the bottleneck is?
In this example there are several things that would go wrong, due to the bottleneck, one of them is the accumulation of products in section A, because if production continues regardless of the slower section B, everything produced In the first section would be queued, which would require a very large space to store, and it would also be stored for a long time waiting to move on to the next section.
How to fix it?
To solve this problem, the first thing to do is size the areas in your company. We explain it to you using the previous example:
In the first phase, a greater number of parts are generated, it may be because the process is simpler or because there are more resources to execute.
While in the painting area the process is longer, the painter must paint the pieces, clean the hoses, the guns and put them in an oven for proper drying. Unlike the first phase, this area is slower by nature. It is essential that you have a complete understanding of your processes in order to start using new work methodologies.
Kanban system
Kanban is a Japanese word that means "visual cards" was devised by Taichi Ohno at Toyota in the early fifties and was born within the framework of the lean manufacturing system, which included concepts such as Just in Time, Kaizen, Poka -Yoke, Muda, among others.
It consists of visually indicating the need to supply or transport necessary material in the different stages of the production processes, seeking to concentrate the highest speed of replacement of parts in the stages that consume the fastest.
By using this system, the storage space that is needed is very little, in addition to that you will buy the material as you progress in the project because you will know when it will be needed. What you consume is what is recorded on your station's kanban card.
The process that handles this system is simple, we explain it to you following the previous example:We already realized that in the metallurgy plant the bottleneck is in phase B, the painting. To release the bottleneck, the number of pieces that are generated per day in each of the phases must be delimited.
It will be explained to the person in charge of phase A that after having welded a certain number of pieces, he will not be able to weld any more until the painter is ready to start painting again. The same will happen in phase B, when a certain number of products has already been painted, the painter will not be able to continue painting until the packer collects these pieces.
With this, a “pull” reaction is generated where the one who sets the pace will be the packer, since if he finishes packing a piece then the painter will be able to start painting another and the welder will be able to weld another piece.
Example of a manufacturing Kanban card.
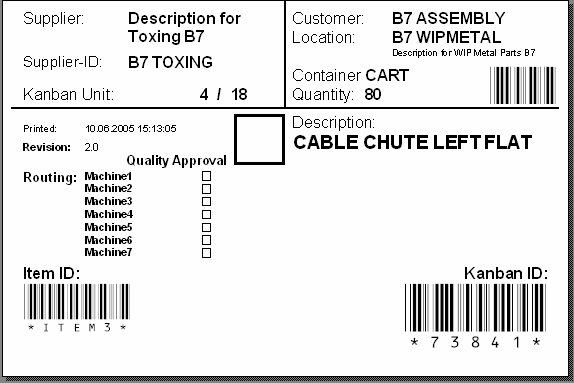
The Kanban approach translated into tasks
On the other hand, there is the Kanban method, developed by David J. Anderson, which was designed mainly for software developments, but currently several companies have adopted it regardless of its line of business.
Anderson based his analysis on the Theory of Constraints and transferred the manufacturing approach, in which bottlenecks appear due to material pending to be processed, to tasks within a workflow.
It was born with the main function of helping companies create and remain with a culture of continuous improvement. One of its main advantages is that it is very visual, since it is a board with cards and columns, it is very easy to understand and anyone can observe the work that is being done.
Each column on the board represents a step in the workflow (Idea, To Do, and Done) and each card represents a work item.
If you see it another way, the pieces are tasks, where from the beginning the task is taken, and they go through it phase by phase until the process is finished and the task is complete.
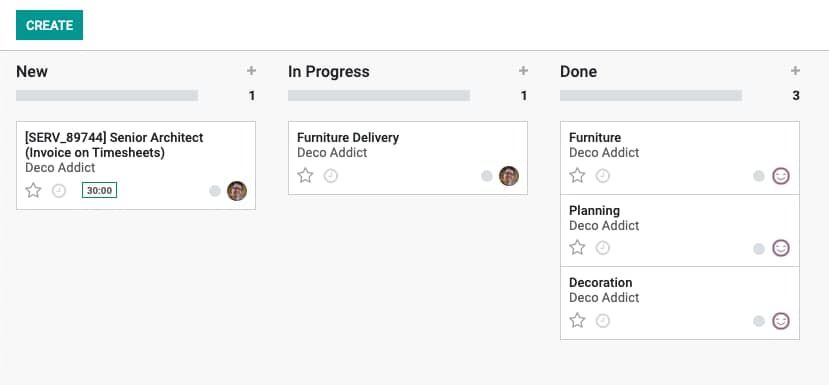
Another advantage of this method is that you can add limits, which are delimited by the number of cards. It defines how many tasks at most can be performed in each phase of the work cycle. This maximum number of tasks is called the WIP (Work In Progress) limit.
For example: if a column has a WIP of three, it means that it is working on three tasks, and it will not be possible to work on any other until one of these three is completed.
Example of a Kanban board.
Kanban principles
Although this method does not use rules, we present some points that you should take into account when carrying it out.
Change the stage until you meet the objective. An obstacle that we go unnoticed in one stage will be more difficult to solve in the next.
Organize the process. To make the stages efficient, it is necessary that each element is prepared to act when necessary.
Design processes correctly. For the Kanban method to be effective, it is necessary that the project phases can be managed individually.
Kanban in Odoo
Odoo has the Kanban method, it allows you to observe the board visually, you can see who is responsible for each task, the priority they have and the hours planned for that task. Each member of the team can move the tasks to where they correspond, it also allows changing the color of each card to view the status of the work and customize them.
Visualizing the workflow on a dashboard, establishing WIP and managing the flow of each task, ensures to make the process easier, since the method is based on an optimization process. It is an effective solution for bottlenecks.
The complete understanding of your processes can help you optimize them in the best way, the Kanban method can be applied to any business sector and is very flexible in terms of changes. Using methodologies that unlock bottlenecks can lead to a much more efficient workflow.
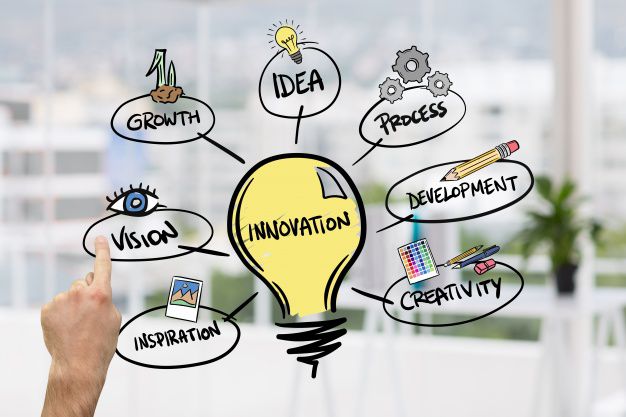